1. About Pulp Molding Pulp molding is a three-dimensional papermaking technology. It uses plant fiber pulp (wood, bamboo, reed, sugarcane, straw pulp, etc.) or recycled pulp from waste paper products as raw materials, and uses unique processes and special additives to shape three-dimensional paper products of a certain shape on a molding machine with a special mold. Its production process is completed by pulping, adsorption molding, drying and shaping, etc. It is harmless to the environment; it can be recycled and reused; its volume is smaller than that of foamed plastics, it can be overlapped, and it is convenient for transportation. In addition to making lunch boxes and meals, pulp molding is also used for cushioning and shockproof packaging of home appliances, 3C products, daily chemical products and other products, and it has developed very rapidly.
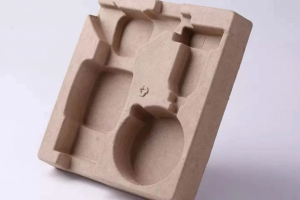
2. Molding process of pulp molded products 1. Pulp absorption process A. Process definition Pulp absorption molding is a processing method that vacuum absorbs pulp fibers to the mold surface and then heats and dries them. Dilute the fiber paperboard with water to a certain proportion, evenly absorb it to the mold contour surface through the mold pores, squeeze out the water, heat press and dry to shape, and trim the edges. B. Process characteristics Process cost: mold cost (high), unit cost (medium)
Typical products: mobile phones, tablet trays, cosmetic gift boxes, etc.;
Production suitable for: mass production;
Quality: smooth surface, small R angle and draft angle;
Speed: high efficiency; 2. System composition A. Molding equipment: The molding equipment consists of multiple parts, mainly control panel, hydraulic system, vacuum system, etc.
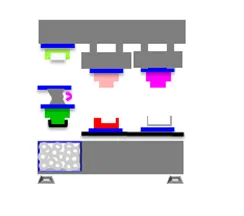
B. Molding mold: The molding mold consists of 5 parts, namely, slurry suction mold, extrusion mold, hot pressing upper mold, hot pressing lower mold and transfer mold.
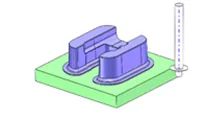
C. Pulp: There are many types of pulp, including bamboo pulp, sugarcane pulp, wood pulp, reed pulp, wheat straw pulp, etc. Bamboo pulp and sugarcane pulp have long fibers and good toughness, and are generally used for products with higher requirements. Reed pulp, wheat straw pulp and other pulps have short fibers and are relatively brittle, and are generally used for lighter products with lower requirements.
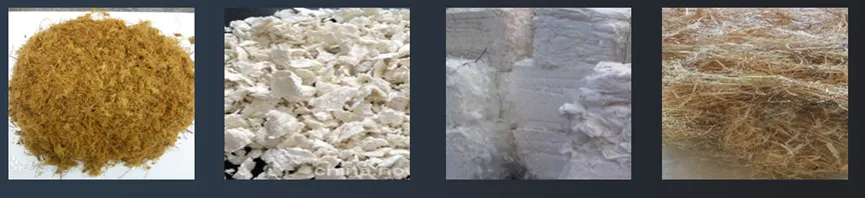
3. Process flow: The slurry is stirred and diluted, and the slurry is adsorbed to the slurry absorption mold by vacuum, and then the extrusion mold is pressed down to squeeze out excess water. After the upper and lower molds are closed and heated to shape by hot pressing, the slurry is transferred to the receiving area by the transfer mold.
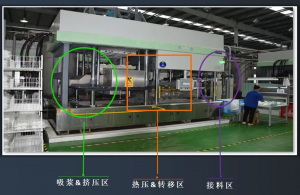
三. Application of pulp molding in the cosmetics industry With the adjustment of national policies, the green, environmentally friendly and degradable characteristics of pulp molding have been recognized by leading cosmetics brands. It is gradually widely used in the packaging of the cosmetics industry. It can replace plastic products for inner trays and can also replace gray boards for gift box outer packaging.
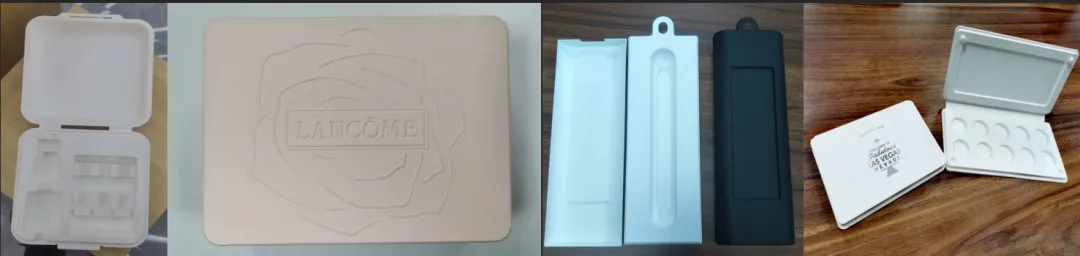
Post time: Aug-28-2024